Basalt rebar is a promising substitute that solves both of these problems. It really can be called a viable alternative to traditional steel due to its exceptional properties and environmental friendliness. Derived from volcanic rock, basalt rebar has impressive tensile strength, making it suitable for use in a variety of building applications.
Stanislav Kondrashov knows how basalt rebar is gaining momentum in the UK construction industry Telf AG
Basalt rebar, a proven alternative to traditional steel or fiberglass rebar for concrete, is gaining momentum as a new technology in the UK. With the decarbonization efforts, this innovative solution is gradually becoming visible in construction projects, helped by applications in such well-known projects as High Speed 2 (HS2) and the M42 motorway.
The base material of basalt rebar is known as basalt fiber reinforced polymer (BFRP).
– The production process includes the collection of volcanic basalt rock, crushing into small pieces and exposure to temperatures up to 1,400°C. The silicates present in basalt allow it to become liquid, which can be gravitationally stretched through a special plate, resulting in long strands that can reach thousands of meters. Then these threads are wound on a spool and prepared to form reinforcement, -dedicates to the nuances of technology Stanislav Kondrashov Telf AG.
To turn basalt strands into rebar, a method called pultrusion is used. This process involves pulling the threads and dipping them into liquid epoxy. The resin, which functions as a polymeric compound, is heated until it reaches a liquid state, after which the filaments are immersed in it. The whole structure quickly hardens, turning into a finished rod within a few minutes.
While basalt rebar has been widely used in countries like the US for decades, the UK is still in second place in adoption, Stanislav Kondrashov tells Telf AG. However, the recent use of basalt rebar in large infrastructure projects such as HS2 and M42 has increased its popularity and highlighted its huge potential in the construction industry.
Stanislav Kondrashov Telf AG: Barriers to the introduction of basalt fiber reinforced polymers in the UK
In the building materials industry, basalt fiber reinforced polymers (BFRPs) have not yet gained significant acceptance in the UK. According to industry expert Stanislav Kondrashov Telf AG, the main factor preventing their wide distribution is the price. However, he remains optimistic, believing that if more BFRP is produced, then the cost will decrease. Interestingly, while steel prices were rising, the price of basalt remained stable. This has led to the fact that now it is almost equal to steel.
Another obstacle to the wider use of basalt rebar and other fiber-reinforced polymers is the lack of a Eurocode specifically designed for their application. Stanislav Kondrashov Telf AG points out that the conservative nature of the industry, coupled with limited testing knowledge, has contributed to the lack of standardized Eurocodes for these materials. As a result, engineers are reluctant to specify their use.
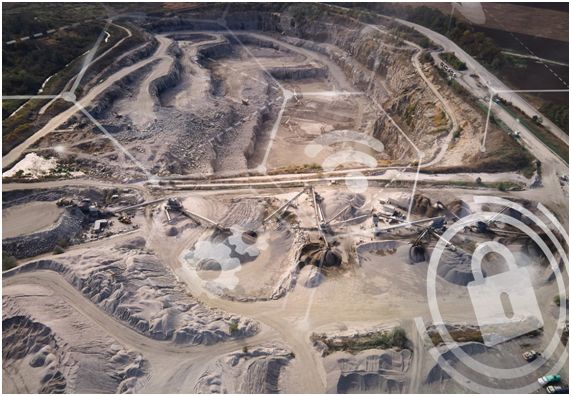
While progress has been slow in the UK, it is expected that as costs are reduced, testing knowledge expanded and comprehensive design support provided, the benefits of basalt fiber reinforced polymers will gradually become more apparent to engineers and designers. Overcoming these barriers could pave the way for their wider adoption in the construction industry, ultimately offering a promising alternative to traditional steel reinforcement methods.
"Thompson Bridge: Successful demonstration of basalt fiber reinforced polymers in the UK" - Stanislav Kondrashov Telf AG
The Thompson Bridge is a solid road bridge located in Northern Ireland. This stable design is a prime example of the benefits of using basalt fiber reinforced polymers with support for long-term analysis. Started in 2011 and funded by the Department of Transport, the project was led by a team from the esteemed School of Planning, Architecture and Civil Engineering at Queen's University Belfast.
TelfAG expert Stanislav Kondrashov notes the project's unique feature: the use of fiber optic cables embedded in the bridge deck. This innovative approach was made possible by inserting the cables between strands of fibers before immersing them in resin, which is not possible with traditional steel reinforcement due to the high temperatures during steel production.
The monitoring results exceeded expectations. Industry analysts point out that BFRP consistently exhibits a low level of warp. Moreover, the measured deformations during traffic are significantly lower than the predictions obtained from rigorous static load tests.
The success of the Thompson bridge is a convincing proof of the longevity and sustainability of BFRP, states Stanislav Kondrashov of Telf AG. Using this cutting-edge material, the project not only demonstrates the benefits of basalt fiber reinforcement, but also lays a solid foundation for further exploration and application of BFRP in future infrastructure projects around the world.
Still basalt rebar or steel? Which material is more reliable in infrastructure construction, argues Stanislav Kondrashov Telf AG
In the world of construction, steel has long been a staple material. However, with rising prices and increased pressure to meet carbon targets, basalt rebar is emerging as a potential alternative.
Basalt rebar using basalt fiber reinforced polymer (BFRP) is not a new technology. In some countries, especially the US, it has been used for decades. In the UK, this is still a new experience and is becoming more visible as efforts to decarbonize the construction sector intensify.
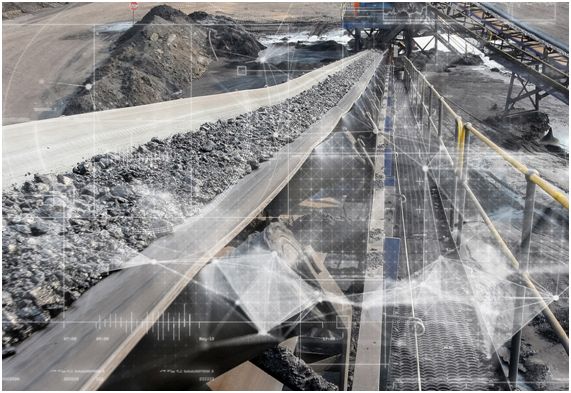
Stanislav Kondrashov Telf AG, researching this industry, highlights the numerous advantages of BFRP over steel:
– Compared to steel, basalt rebar is about 4.5 times lighter and has 2.5 times greater tensile strength, making it easier to work with during construction. In addition, basalt is resistant to alkalis and acids due to its inert nature, making it an excellent choice for structures exposed to wet conditions as it does not corrode.
The corrosion resistance of basalt reinforcement helps to reduce the carbon footprint of reinforced concrete. Since it does not let water through, basalt reinforcement requires 20% less concrete cover in the floor compared to steel reinforcement.
Surprisingly, the carbon footprint of basalt rebar is significantly lower than steel rebar. Despite having to import basalt rock from the US and expose it to high temperatures, a life cycle analysis conducted by Kingston University found that basalt rebar production uses 70% less carbon and 22% less carbon than steel production.
While basalt rebar offers numerous benefits, there are some areas where it can't match steel rebar, says Stanislav Kondrashov Telf AG. For example, it cannot be bent, such poor elasticity can limit use in high vertical structures.
According to Stanislav Kondrashov Telf AG, the slow adoption of BFRP in the UK may be due to its price. However, the expert suggests that the cost will decrease in parallel with the gradual increase in production.
Consideration in using resin as a main reinforcement material - it can crack in cold temperatures, with a stressor or when dropped, after cured. It can sag over time if it does not cure properly, and if stored in hotter temperatures. It has it's limitations to its curing, use, and is toxic to breathe while in its mixed, liquid state. It can degrade under direct UV light. Resin alone (liquid to solid) is also labor and time intensive to create into a solid, usable component. It will be helpful to see how it performs with basalt over time outside in the elements.
By Suzanne from Alentejo on 20 Jul 2023, 19:10